Dr.Jass
Pastor of Muppets
Yesterday when I got home, there was a box on my porch from Van's Auto LLC, a small WI-based resto parts outfit that employs the guy who bought my 340 Challenger back in '89. 'Twas my new repro dash defroster vents. I'd expected to have new tubing for them today, but one of our warehouse guys screwed up so I won't have that until tomorrow. Regardless, I decided to be prepared for its arrival and get the vents handled tonight. This, I'm certain, will come back to bite me in the ass tomorrow.
I started by using SEM's Plastic and Leather Prep, which is a cleaner/adhesion promoter for painting vinyl and plastic. Then I sprayed the vents with the closest color-match paint available for this interior which, of course, is a closer match to the interior's lighter blue.
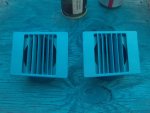
Why bother with the defroster vents in a thinly-veiled race car? Beater or not, I want everything present on the car to not only work, but work correctly. On an A-body, the defroster outlets are also the only thing that disperses the airflow across the windshield, and ones that look like this ain't dispersing a damned thing:
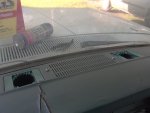
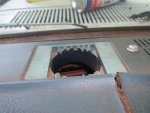
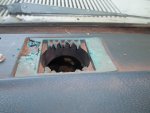
Those pictures were taken prior to my even starting... they were that bad when I got Agnes. The black defroster vents are not as prone to this kind of catastrophic failure, but after 50+ years in the blazing sun under glass, they're usually not so great. The color-matched ones? Expect them to look similar. Also, expect them to literally crumble as you work. Have the shop vac handy; you're gonna need it. The vents are retained by three molded-in plastic "studs" per vent, each with a thread-cutting nut. We'll revisit those nuts later.
This is the mess you can expect once you've got the nuts removed, or just as likely, the studs ripped out of the vents:
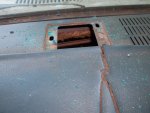


A close-up of just how crumbly this plastic gets after five decades. Mind you, I made no attempt to damage or destroy these to ease their removal, all I did was turn the nuts:
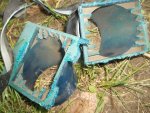
See the ridiculous angle at which those tubes are oriented? The studs are angled exactly the same rather than pointing face down. In an attempt at serviceability, Chrysler did this so that the vents can be removed/installed without removing the windshield. No joke--if those tubes were straight, the glass would have to come out to service or replace the vents!
The problem, or the problem as it exists now, is that though the mounting studs or pins are angled, the underside of the dash is not. This means that the nuts, as they cut their threads, have to start at an angle and work themselves to finish flush with a non-angled surface. And this is why I said we'd revisit the nuts.
Simply put, the new dash vents don't just fall into their recesses. In fact, they fight you all the way down. They will not fit flush, I'm here to tell you. What you end up doing is trying to start the nuts on studs that are barely through the dash. They won't. Then you'll want to pound on the vents to get them to seat, which is fine if A) you don't mind wasting $50 by destroying your brand-new vents, B) your car has a black dash and there's no risk of damaging the fresh paint (repros are only available in black), and C) you're attempting to use the supplied, visually-identical thread-cutters supplied with the vents.
Hear me now, listen to me well, and remember this forever: DO NOT DISCARD THE ORIGINAL NUTS. They are orders of magnitude better than the new ones. The difference is beyond belief. You will fight with the replacement nuts: they won't start, they'll fall of the studs repeatedly (conveniently landing in the ledge on the bottom of the dash), and you will rue the fact that you started this project. You will say words of which Mother would not be proud. You will curse the idiot engineer who put those studs on that angle and possibly insult his gene pool.
Then, when the new nuts are scattered aboot (or in my case, three are installed (not all on the same vent) after nearly an hour of fighting, the nearest nut will be a factory one--all the others are trapped somewhere in the dash--and you'll try starting it with your fingers because damn it, you're tired of trying to hold that socket on that angle and trying to twist it. The clouds will part, a particular beam of sunshine will illuminate your car, and Heaven's choir will sing, "Ahhhhhhhhhh!" Original nut starts with your fingers--impossible with the repros. Easily turned with a socket, then later a ratchet. Pulls the vent flush in its recess like it's no big deal and the nut makes its turn and flattens against the dash--exactly as engineered, and easy as pie. Literally the toughest factory nut I installed was five times easier than the easiest repro that came with the vents. The original engineer was probably a pretty-cool guy after all, and you'd maybe like to shake his Dad's hand, now that you've used the actual nuts he specified. Incredible.
Son of a bitch, they pulled right in. Ain't that some shit:
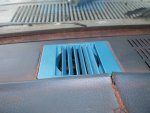
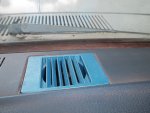
Again, I can't stress enough how much easier this is using the original hardware. You'll go from "ready to give up" to "I could've been done an hour ago" in very short order. Though I didn't do a close-up examination, in the hand the nuts look identical other than patina. I can only assume the OE ones have a sharper thread-cutting edge on them; if you're lacking the original nuts I'd suggest trying to sharpen the replacement nuts' cutting edges with a small rat-tail file. Or--and I'm not kidding--sourcing some original nuts, even if you have to lie on your back in a junkyard and remove a set from a different car.
Still not connected to anything, but at least this part is done:
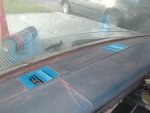
With the windshield mitigating the flash, the mismatch isn't quite so horrible:
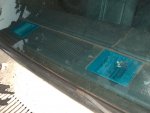
A couple of thoughts on the significant difference in the colors:
First, the original vents were actually almost equally bad in the mismatch department. It's hard to match a molded-in color to a painted surface; anyone who's ever done plastic scale models will be familiar with the issue.
Next, the dash is dusty, dirty, faded and sunburnt. It's nearly 52 years old and I did nothing to rejuvenate it. All I did was vacuum the plastic crumbs from the old vents. The paint, on the other hand, is literally hours old in the picture. To be honest, I knew it wasn't right before I started because I'd already done the steering column with it. As such...
My experience with this particular paint--marketed by OER--is that it darkens with time. That's not uncommon, and I also believe sunlight burns some of this particular blue's "brilliance" off with time. The steering column is a much-closer match to the dash around it these days than it was when I installed it--something you can verify by going back through this thread.
My own concerns are covered: They're in, they're blue, and the defroster/defogger will work as designed. The A-body design is not a spectacular one, but it works well enough... much better than the two peepholes the old vents created.
I started by using SEM's Plastic and Leather Prep, which is a cleaner/adhesion promoter for painting vinyl and plastic. Then I sprayed the vents with the closest color-match paint available for this interior which, of course, is a closer match to the interior's lighter blue.
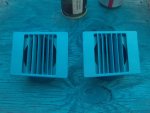
Why bother with the defroster vents in a thinly-veiled race car? Beater or not, I want everything present on the car to not only work, but work correctly. On an A-body, the defroster outlets are also the only thing that disperses the airflow across the windshield, and ones that look like this ain't dispersing a damned thing:
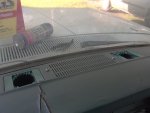
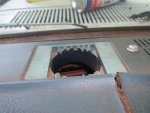
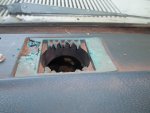
Those pictures were taken prior to my even starting... they were that bad when I got Agnes. The black defroster vents are not as prone to this kind of catastrophic failure, but after 50+ years in the blazing sun under glass, they're usually not so great. The color-matched ones? Expect them to look similar. Also, expect them to literally crumble as you work. Have the shop vac handy; you're gonna need it. The vents are retained by three molded-in plastic "studs" per vent, each with a thread-cutting nut. We'll revisit those nuts later.
This is the mess you can expect once you've got the nuts removed, or just as likely, the studs ripped out of the vents:
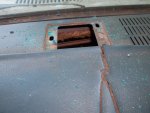


A close-up of just how crumbly this plastic gets after five decades. Mind you, I made no attempt to damage or destroy these to ease their removal, all I did was turn the nuts:
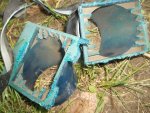
See the ridiculous angle at which those tubes are oriented? The studs are angled exactly the same rather than pointing face down. In an attempt at serviceability, Chrysler did this so that the vents can be removed/installed without removing the windshield. No joke--if those tubes were straight, the glass would have to come out to service or replace the vents!
The problem, or the problem as it exists now, is that though the mounting studs or pins are angled, the underside of the dash is not. This means that the nuts, as they cut their threads, have to start at an angle and work themselves to finish flush with a non-angled surface. And this is why I said we'd revisit the nuts.
Simply put, the new dash vents don't just fall into their recesses. In fact, they fight you all the way down. They will not fit flush, I'm here to tell you. What you end up doing is trying to start the nuts on studs that are barely through the dash. They won't. Then you'll want to pound on the vents to get them to seat, which is fine if A) you don't mind wasting $50 by destroying your brand-new vents, B) your car has a black dash and there's no risk of damaging the fresh paint (repros are only available in black), and C) you're attempting to use the supplied, visually-identical thread-cutters supplied with the vents.
Hear me now, listen to me well, and remember this forever: DO NOT DISCARD THE ORIGINAL NUTS. They are orders of magnitude better than the new ones. The difference is beyond belief. You will fight with the replacement nuts: they won't start, they'll fall of the studs repeatedly (conveniently landing in the ledge on the bottom of the dash), and you will rue the fact that you started this project. You will say words of which Mother would not be proud. You will curse the idiot engineer who put those studs on that angle and possibly insult his gene pool.
Then, when the new nuts are scattered aboot (or in my case, three are installed (not all on the same vent) after nearly an hour of fighting, the nearest nut will be a factory one--all the others are trapped somewhere in the dash--and you'll try starting it with your fingers because damn it, you're tired of trying to hold that socket on that angle and trying to twist it. The clouds will part, a particular beam of sunshine will illuminate your car, and Heaven's choir will sing, "Ahhhhhhhhhh!" Original nut starts with your fingers--impossible with the repros. Easily turned with a socket, then later a ratchet. Pulls the vent flush in its recess like it's no big deal and the nut makes its turn and flattens against the dash--exactly as engineered, and easy as pie. Literally the toughest factory nut I installed was five times easier than the easiest repro that came with the vents. The original engineer was probably a pretty-cool guy after all, and you'd maybe like to shake his Dad's hand, now that you've used the actual nuts he specified. Incredible.
Son of a bitch, they pulled right in. Ain't that some shit:
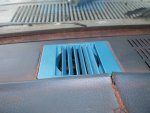
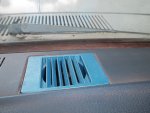
Again, I can't stress enough how much easier this is using the original hardware. You'll go from "ready to give up" to "I could've been done an hour ago" in very short order. Though I didn't do a close-up examination, in the hand the nuts look identical other than patina. I can only assume the OE ones have a sharper thread-cutting edge on them; if you're lacking the original nuts I'd suggest trying to sharpen the replacement nuts' cutting edges with a small rat-tail file. Or--and I'm not kidding--sourcing some original nuts, even if you have to lie on your back in a junkyard and remove a set from a different car.
Still not connected to anything, but at least this part is done:
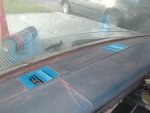
With the windshield mitigating the flash, the mismatch isn't quite so horrible:
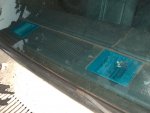
A couple of thoughts on the significant difference in the colors:
First, the original vents were actually almost equally bad in the mismatch department. It's hard to match a molded-in color to a painted surface; anyone who's ever done plastic scale models will be familiar with the issue.
Next, the dash is dusty, dirty, faded and sunburnt. It's nearly 52 years old and I did nothing to rejuvenate it. All I did was vacuum the plastic crumbs from the old vents. The paint, on the other hand, is literally hours old in the picture. To be honest, I knew it wasn't right before I started because I'd already done the steering column with it. As such...
My experience with this particular paint--marketed by OER--is that it darkens with time. That's not uncommon, and I also believe sunlight burns some of this particular blue's "brilliance" off with time. The steering column is a much-closer match to the dash around it these days than it was when I installed it--something you can verify by going back through this thread.
My own concerns are covered: They're in, they're blue, and the defroster/defogger will work as designed. The A-body design is not a spectacular one, but it works well enough... much better than the two peepholes the old vents created.
Last edited: