Dr.Jass
Pastor of Muppets
That transmission is pretty & all, but it ain't worth a damn without a shifter. Once again, this would not go as easily as hoped.
First and foremost, the case/tailshaft housing I used were from a 1968 A-body. An early '68, in fact... so the shifter mount was actually for an Inland. No, you can't put a Hurst on it. "Big deal, just switch it out!" you yell. If only it were that easy. The bolts were stuck so badly that I never disturbed the mount during the rebuild--I just masked it off when I painted it. Now it was in the car, and still schtuck güt. Out came the cutoff wheel, chisel, hammer, and prayer. It worked.
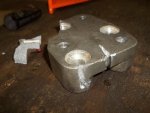
The next wrong part on hand was the Super Shifter I, which turned out to be for an E-body (I guess we know where that will go). I started digging through my stash of shifters, and didn't have one. I found one with the right A-body operating levers still bolted to a flanged-output A-body trans I bought for $100 at Jefferson. Much to my chagrin, it was rusted solid. After not-significant soak time, I still had to put it in a vise and literally beat the mechanism out of the case.
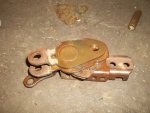
Further disassembly required prying some of those pieces apart... but I finally had it completely apart, ready to be cleaned and rebuilt.
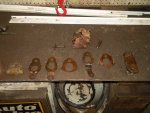
There would be another challenge inside. Apparently the last user of this shifter was a retarded silverback gorilla. So much for the overstop bolts.

I had to pry apart the shifter case to remove the side panel for access. After that, a wee bit of grinding... and problem solved.
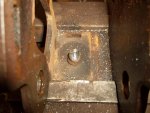
Since I was working alone, I did not document the reassembly process. I bolted the mechanism to the sorta-right shifter mount scapped from one of Stretch's overdrives, already in place on the transmission. Then I grabbed the too-nice-for-this-car OE A-body Hurst handle graciously donated to this project by restoman (thank you yet again!) and slipped the boot on it before bolting it to the shifter. I threaded on the OE-style white knob and installed the boot. Now we've got a proper-looking office, other than the erupted bench seat.
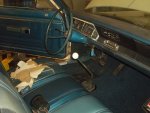
Shifter in the 1st/3rd-gear position:

And then in the 2nd/4th-gear location:

The shifter's operation is buttery smooth, as one would expect. There's still no linkage on it, as the reproduction stuff I bought doesn't seem to fit. I know it's the right shifter and the F-body mount is very, very close to the A-body one, but no matter the orientation it binds. I have some early A-body linkage that seems like it'll work, but I think I'm going to bite the bullet and buy new linkage from Brewer's. The gold-irridited, plastic-bushed (!) stuff sold by PG Classic and others is not worth the effort, at least not for the A-bodies. Skip it. The rods only work with the bushings provided, as do the transmission levers. The bushings do not interchange with Hurst parts, either, so once they're beat--and that won't take long, judging by their feel--you're on your own. You were warned. I have a set of that stuff for my Challenger, too, and another set for Stretch's Valiant shifter. All 3 sets will likely end up on eBay, whether the Challenger stuff fits or not. The Brewer stuff appears to be right.
It's starting to look like an actual car now!
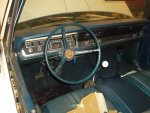
First and foremost, the case/tailshaft housing I used were from a 1968 A-body. An early '68, in fact... so the shifter mount was actually for an Inland. No, you can't put a Hurst on it. "Big deal, just switch it out!" you yell. If only it were that easy. The bolts were stuck so badly that I never disturbed the mount during the rebuild--I just masked it off when I painted it. Now it was in the car, and still schtuck güt. Out came the cutoff wheel, chisel, hammer, and prayer. It worked.
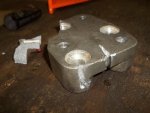
The next wrong part on hand was the Super Shifter I, which turned out to be for an E-body (I guess we know where that will go). I started digging through my stash of shifters, and didn't have one. I found one with the right A-body operating levers still bolted to a flanged-output A-body trans I bought for $100 at Jefferson. Much to my chagrin, it was rusted solid. After not-significant soak time, I still had to put it in a vise and literally beat the mechanism out of the case.
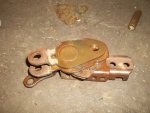
Further disassembly required prying some of those pieces apart... but I finally had it completely apart, ready to be cleaned and rebuilt.
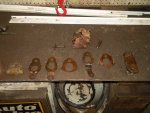
There would be another challenge inside. Apparently the last user of this shifter was a retarded silverback gorilla. So much for the overstop bolts.

I had to pry apart the shifter case to remove the side panel for access. After that, a wee bit of grinding... and problem solved.
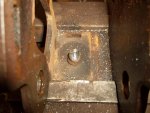
Since I was working alone, I did not document the reassembly process. I bolted the mechanism to the sorta-right shifter mount scapped from one of Stretch's overdrives, already in place on the transmission. Then I grabbed the too-nice-for-this-car OE A-body Hurst handle graciously donated to this project by restoman (thank you yet again!) and slipped the boot on it before bolting it to the shifter. I threaded on the OE-style white knob and installed the boot. Now we've got a proper-looking office, other than the erupted bench seat.
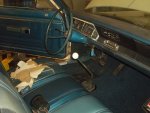
Shifter in the 1st/3rd-gear position:

And then in the 2nd/4th-gear location:

The shifter's operation is buttery smooth, as one would expect. There's still no linkage on it, as the reproduction stuff I bought doesn't seem to fit. I know it's the right shifter and the F-body mount is very, very close to the A-body one, but no matter the orientation it binds. I have some early A-body linkage that seems like it'll work, but I think I'm going to bite the bullet and buy new linkage from Brewer's. The gold-irridited, plastic-bushed (!) stuff sold by PG Classic and others is not worth the effort, at least not for the A-bodies. Skip it. The rods only work with the bushings provided, as do the transmission levers. The bushings do not interchange with Hurst parts, either, so once they're beat--and that won't take long, judging by their feel--you're on your own. You were warned. I have a set of that stuff for my Challenger, too, and another set for Stretch's Valiant shifter. All 3 sets will likely end up on eBay, whether the Challenger stuff fits or not. The Brewer stuff appears to be right.
It's starting to look like an actual car now!
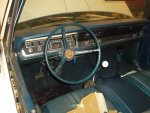