A bit of a lazy weekend...
Thursday the weather wasn't cooperative, so I didn't spend any time on the car. Friday, the new tach arrived and to my surprise it was smaller than expected. I found a new tach cup lying around, and there was no way the tach would fit it--it was way too small. I went outside and grabbed a Track Force pedestal tach from the garage, and that cup was also too large (the bezel was part of the tach movement/face anyhow). The new tach had come with a dash mounting bracket, but it was retained by a single machine screw, so I looked at the tach currently hanging from the dash--the one in previous photos that's been problematic for me. Thinking "there's no time like the present," I managed to figure out how to get the bezel and lens/spacer off, and disassembled the old unit. 'Twas then I discovered my wiring error (see the "Goofy Tach" thread). With the cup gutted, it was time to see if I could make the "new" tach work.
The case is a three-piece affair, the key part being the rear cup that also incorporates the tach half of the mount. It has a single bolt hole and is black plastic (the main body and bezel are chromed steel). Clearance is tight (especially the bulb socket), but the Stage III tach bolts into the rear cup using the screw from the old tach guts in the original hole. Halfway home.
There are two tabs on the main body that mount the old circuit board. There was no provision on the Stage III, and in fact they limited the rearward travel enough that the rear cup couldn't be assembled to the main body. I simply bent those out of the way, determined where the tach body needed to sit, then bent them again so they're now folded over the rear of the tach body to hold it in position. Once I'd done that, the bezel snapped into place without the old lens or spacer. The bezel fits over the Stage III's bezel like it was born there, and since the Stage III has an integral lens there was no issue... other than the redline. It's not externally adjustable. No big deal; I wanted to rewire the tach and slightly modify the bulb socket for extra clearance anyhow.
Sneak preview... this was taken later, but it shows that my creation could almost pass for a factory-assembled unit:
Yes, that's rust around the outside edge, behind the tach lens. It's Agnes... you thought I'd spring for NOS?! It was $40 and guaranteed to work. The corrosion adds character.
Since the tach was down, and it's a pain in the arse to mount, Staruday was a good time to install the new factory temperature gauge in the cluster. Despite starting quite late, down came the column, out came the cluster, and with a few more nuts I had the burned temperature gauge out. I set it next to the NOS unit, and contacted Houston ground control. The problem? Apparently, older cars used fluorescent orange needle paint, where I'd thought they were faded and used fluorescent red on the other needles when I repaired and freshened the cluster. The little bit of mismatch is the kind of thing that would bother me to no end, even though with the cluster assembled it's much less obvious. Smoked gauge is on the left, evidenced by my paint overrun.
I rounded up my needle paint and proceeded to do a much-neater job on the new gauge. Seemed a sin to paint an NOS gauge, but it was a lot less effort than repainting all the other pointers. They all match, which is all that matters to me:
With the cluster apart, my freshly-detailed lenses didn't seem so fresh anymore. Glass cleaner had no effect, and upon close inspection I realized the "dust" was white overspray from painting the floors. Out came the Mother's Mag & Aluminum polish--I can't recommend this stuff enough--and with some time and elbow grease the lenses look as good as really-good used... "new" would require disassembing the bezel, and it's not designed nor intented to be taken apart. It's heat-staked together, and I'm not making that kind of effort. I reassembled the cluster and connected the headlamp switch and ammeter leads, then called it a day.
Today involved blowing the tach apart for wiring and socket modification. I'd left the cluster out because the tach is much easier to wire through the cluster hole, despite being largely plug-and-play due to my jumper harness (the tach-signal wire
is solid to the bulkhead disconnect, so it required solder/heat shrink). Before reassembly, I wanted to see if I could match the tach lighting to the dash, so I installed an AutoMeter green bulb filter (condom). It didn't
quite cover the bulb's glass, so I put a heat-shrink "collar" on the part of the bulb not covered. Reassembly was straightforward, other than the time-consuming bit of running the new wiring through the old sleeving and soldering terminals recycled from old factory harnesses. Fishing all of it through the hole I drilled behind the radio/heater bezel wasn't particularly fun, but once I did I let the tach hang by its wires so I could reinstall the cluster... which I did. The steering column was bolted back up, and while I was lying down on the job I decided to install the two remaining bulb condoms on the aftermarket oil pressure and temperature gauges.
The office is all back to normal, with the new furnishings fitting in nicely:
After dark, I went out and checked to see how the filtered bulbs worked. Despite being nowhere near the same color as the factory cluster's built-in bulb filters, the AutoMeter covers provide a very-close match to the factory illumination... a pleasant surprise.
Tomorrow the new rocker-shaft bolts arrive. Fingers crossed... and Agnes is anxious to get 'em.
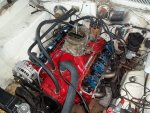